REDUCCION DEL TIEMPO DE CAMBIO DE FORMATO EN LAS MAQUINAS ENVASADORAS DE DETERGENTES B3 Y T1 DE LA EMPRESA UNILEVER ANDINA BOLIVIA S.A. APLICANDO LA HERRAMIENTA SMED
Tutor | Semestre | Modalidad | Categoria | |
---|---|---|---|---|
ING. XIMENA TRIVEÑO GUTIERREZ | II-2018 | adri.laime@hotmail.com | PROYECTO DE GRADO | INGENIERIA DE METODOS |
improvement analysis line company control product method time process production
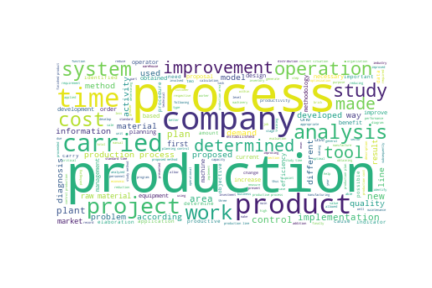
Resumen
La herramienta desarrollada de SMED, permitió reducir el tiempo de cambio de formato en las máquinas envasadoras de detergentes B3 y T1 de la empresa Unilever Andina Bolivia S.A., lo cual ayudó a mejorar la eficiencia de cada máquina y disminuir los costos por parada, mejorando la productividad, tras el desarrollo de los 7 pasos de la herramienta. Primeramente se realizó el paso 0 con el desarrollo de 5 actividades preliminares, donde se analizó la matriz de costos, en la cual se cuantifican las 39 pérdidas que reconoce la filosofía de World Class Manufacturing, donde el changeover time (tiempo de cambio), es identificada como la tercera pérdida más grande. Se estratificaron las pérdidas según su valor monetario, donde se observa que la línea T1 registró la mayor pérdida con 81 814 euros, seguida de la línea T2 con 74 045 euros y posteriormente de la B3 con 19 014 euros, todo durante la gestión 2 017, luego se estratificó la pérdida de changeover time, considerando que se tienen dos tipos de cambio, de formato y de variedad. El área de envasado detergentes, cuenta con 6 máquinas envasadoras, de las cuales 3 realizan el cambio de formato, la línea T1, T2 y B3, y todas realizan el cambio de variedad. En éste proyecto se implementó la herramienta de SMED, para reducir los tiempos en la línea T1 y B3, como la línea T2 tiene el mismo principio de funcionamiento que la T1, todo lo que se desarrolló en la T1 se replicará en la T2. La segunda parte de la estratificación es cuando se identifica el lugar que ocupa la pérdida de cambio en el árbol de pérdidas, en las máquinas envasadoras se generan 21 pérdidas, dentro la cual se tiene a la pérdida 11 de changeover (cambio), que es la tercera pérdida más grande la línea T1, registrando un valor de 3,06%, ésta se subclasifica en cambio de formato con 0,90% y cambio de variedad con 2,16%, en la línea B3, es la quinta pérdida más grande con 2,29%, en cambio de formato con 1,43% y cambio de variedad con 0,86%. Las demás pérdidas son atacadas por otros grupos de mejora.Después, se determinó la secuencia para identificar que formato se realiza con mayor frecuencia en ambas máquinas, en la línea T1 se trabajó con los formatos de 800 y 200 gramos, en la línea B3 con los formatos de 4 y 2,3 kilogramos, se buscaron referencias sobre los estándares de tiempo de cambio de formato, donde según estándares oficializados se tiene a la línea T1 con 90 min de duración del cambio y a la línea B3 con 150 min de duración. Para la validación de éstos tiempos estándares, y conocer a detalle cada una de las tareas que comprende el cambio de formato, se realizó y aplicó el Go to the Gemba (ir a la planta) para culminar el desarrollo de las actividades preliminares.En seguida se desglosan los 7 pasos de SMED, en el paso 1 se definió las líneas a ser estudiadas que son las líneas B3 y T1, como paso 2 se conformó el equipo multidisciplinario de SMED, el cual estuvo compuesto por el supervisor de producción, de mantenimiento, de WCM y 2 operadores de envasado, como paso 3 se mapearon las líneas a estudiar, el paso 4 donde se aplicó las 4 fases de la filosofía de SMED, que es el paso clave para garantizar la reducción del tiempo, se realizó un diagnóstico de la situación actual como fase 0, para verificar los tiempos de duración del cambio en las líneas T1 y B3, donde los tiempos registrados fueron de 158 y 142 min, además de identificarse el número de tareas en cada una, contabilizando 33 y 31 tareas respectivamente, y también cuantificando la distancia que el operador se desplaza. En la fase 1 se externalizaron tareas que pueden ejecutarse mientras las máquinas aún sigue funcionando, y se separaron las que pueden ejecutarse antes del cambio (Pre-changeover) o después del cambio (Post-changeover), es así que en la línea T1 se externalizaron 10 tareas, 6 Pre-changeover y 4 Post-changeover, quedando 23 tareas como internas del total de 33, reduciendo el tiempo en 30 min por lo que el nuevo tiempo de cambio era de 128 min, en la línea B3 se externalizaron 7 tareas, 5 Pre-changeover y 2 Post-changeover, quedando 24 tareas como internas del total de 31, reduciendo el tiempo en 27 min por lo que el nuevo tiempo de cambio era de 115 min.La fase 2 del streamline de tareas internas y externas usando la metodología ECRS, nos permitió realizar mejoras en cada una de las tareas, para seguir reduciendo el tiempo de las mismas, es así que en la línea T1 se eliminó 1 tarea, se combinaron 11, se redujeron 12 y se simplificaron 10, reduciendo el tiempo en 60 min más al total de 128 min, reduciendo el tiempo de duración del cambio a tan solo 68 min. En la línea B3 se eliminó 2 tareas, se combinaron 6, se redujeron 8 y se simplificaron 11, reduciendo el tiempo en 24 min más al total de 115 min, reduciendo el tiempo de duración del cambio a 91 min. Finalmente se realizaron mejoras en los ajustes de la fase 3, para facilitar las tareas. Luego se desarrolló el panel de SMED, en el que se expuso todo lo desarrollado con la herramienta, una vez culminadas y definidas las mejoras, se realizó el entrenamiento del personal en el nuevo orden. Se monitorearon los cambios, en los cuales se verificó, que el tiempo de cambio de formato en la línea T1 puede realizarse en 71 min, teniendo una reducción total de 87 min con respecto al total de 158 min. La línea B3 puede realizarse en 120 min, y con la continuación de las mejoras puede realizarse hasta en 91 min, teniendo una reducción inicial de 22 min y posteriormente una reducción total de 51 min al total de 142 min, en base al menor registro en el que se realice el cambio de formato, se definieron los nuevos tiempos estándares, garantizando siempre la comodidad y facilidad del desarrollo de las tareas realizadas por el operador. Es así que la inversión total que el proyecto solicitará para su implementación es de 11 030,50 Bs, dentro de los indicadores se tuvo un VAN de 26 620,19 Bs, un TIR de 81,00%, una TMAR de 22,49% y por último el rendimiento sobre la inversión que era de 3,37 Bs, que se obtiene por cada boliviano del capital invertido, todo en la línea T1. La inversión en la línea B3 es de 11 774,00 Bs, dentro de los indicadores se tuvo un VAN de 903,30 Bs, un TIR de 26,00%, una TMAR de 22,49% y por último el rendimiento sobre la inversión que era de 1,08 Bs, que se obtiene por cada boliviano del capital invertido. El costo de implementación fue de 251,29 Bs. La implementación de todo el proyecto permitirá mejorar los indicadores de eficiencia como la OEE% y la productividad en cada máquina.
Palabras clave
CHANGEOVER TIME, SINGLE MINUTE EXCHANGE OF DIE, WORLD CLASS MANUFACTURING, PRODUCTIVIDAD, MANUFACTURA, EFICIENCIA, COSTOS.
Metricas del proyecto de grado
Visualizaciones: 5
Agregados a favoritos: 0
Proyectos de grado similares