REDUCCION DEL TIEMPO EN LOS CAMBIOS DE CALIBRE DE LA LINEA DE PRODUCCION DE PLANTA SACABA SD, PEPSIAPLICANDO HERRAMIENTAS DE LA METODOLOGIA SMED
Tutor | Semestre | Modalidad | Categoria | |
---|---|---|---|---|
ING. JUAN RUBEN GARCIA MOLINA | II-2020 | jpanozosejas@gmail.com | PROYECTO DE GRADO | INGENIERIA DE METODOS |
improvement analysis line company control product method time process production
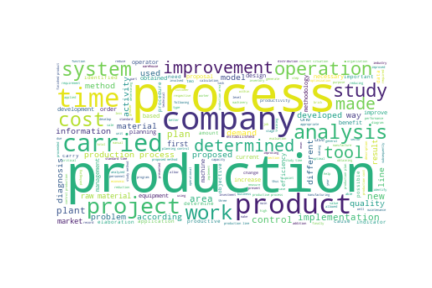
Resumen
En la actualidad, el consumo de bebidas ultra procesadas en Bolivia aumentó en 105% según la OPS, lo que genera un aumento de la demanda de gaseosas e impulsa la diversificación de tamaños en sus presentaciones. La planta de gaseosas “Sacaba SD” la cual pertenece a CBN tiene como una meta el aumento de la producción en un 2,2% anual. La planta presentó ciertas deficiencias a nivel de envasado las cuales generaron tiempos de paradas largos, entre estos tiempos, se encuentraron los tiempos por cambios de calibre. Se realizó un análisis de los tiempos de cambios de calibre, mediante dicho análisis se determinó que estos representan un 15,61% de todos los tiempos de paradas programadas, es decir, paradas de la línea de envasado que están programados en el plan de producción. Estas pérdidas de tiempo afectaron en la producción de las bebidas y reducian la productividad y eficiencia de la planta. Para la reducción de estos tiempos de cambio de calibre se implementó herramientas de la metodología SMED. Se realizó un análisis de datos del mix de produccion de la empresa, en el que se cuantificó los cambios de calibre más recurrentes, siendo estos los cambios de 3 litros a 2 litros, de 2 listros a 3 litros, de 0,5 litros a 3 litros y de 3 litros a 1 litro. Luego de determinar los cambios más recurrentes se procedió a determinar el número de observaciones para poder determinar el tiempo estándar, el método utilizado para determinar el tiempo estándar fue el método estadístico explicado en el libro de Ingenieria Industrial de Niebel, para el cual fue necesario realizar un estudio preliminar de tomar 10 observaciones preliminares, para determinar el número de observaciones. Luego de determinar el número de observaciones, se procedió a tomar los valores de dichas observaciones para cada punto de la línea de envasado los cuales fueron representados por la maquina y su respectiva función función (Etiquetadora, Enjuagadora de botella, Llenadora 1, Capsuladora 1, Conjunto blocado, Termocontraibles) y se halló el tiempo promedio de esos valores, posterior a esto se determinó el ritmo de trabajo de los operadores titulares de cada punto de la línea de envasado utilizando el sistema desarrollado por la Westing House Electric Corporation para poder tener el tiempo estándar de cambio de calibre por cada punto de la línea de envasado, además se estableció los procedimientos (Pasos) de cambio de calibre para cada punto, con su respectivo tiempo estándar de todo el procedimiento al igual que para cada paso de los procedimientos establecidos. Se realizó la implementación de las herramientas de la metodología SMED, pero previamente a eso, se determinó un equipo SMED conformado por operadores, técnicos, analista SMED y jefes, luego se determinó los puntos críticos del proceso de cambio de calibre de acuerdo a su tiempo estándar de cambio de calibre teniendo como puntos críticos Llenadora 1 con un tiempo de 162,22 minutos, Termocontraibles con unos tiempos de 121,9 minutos y 72,77 minutos y el conjunto blocado un tiempo de 78,62 minutos. Posteriormente realizó un análisis del procedimiento estándar de cada punto de la línea de envasado, en los cuales se clasificó los tipos de desperdicios existentes en el procedimiento según los 8 tipos de desperdicios, además se identificó los pasos en los cuales se clasificó entre externos (no es necesario que la maquina este parada para realizarlo) e internos (es necesario que la maquina este parada para realizarlo). Con los pasos que se clasificaron como internos, algunos se procedierón a externalizarlos, es decir, se los convirtió en actividades externas para poder realizarlas cuando la maquina siga en funcionamiento y no sea necesario pararla, como el transporte de algunos formatos al puesto de trabajo antes del inicio del proceso de cambio de calibre, preparación de insumos, lavados de formatos, entre otros pasos de los procedimientos de cambios de calibre. Una vez externalizados los pasos que se clasificaron como internos, se realizó el análisis ECRS (Eliminar, Combinar, Reducir, Simplificar) a cada punto de la línea de envasado, determinando las acciones para los pasos en los que se puedan eliminar, combinar, reducir o simplificar los desperdicios encontrados mediante el análisis de los 8 desperdicios. Con todas las propuestas de mejoras de la externalización y el ECRS se determinó las inversiones que se realizaron como ser la fabricación de carritos de cambio de calibre, las estaciones de trabajo, los separadores para las termocontraibles, los centradores fijos y el cambio de ajuste a ajuste sencillo de los tubos de venteo de la llenadora 1, dando una inversión en activos fijos de 64.360 Bs, además se determinó otra inversión de capital de trabajo con un valor de 482.687,325 Bs y con un costo de capacitaciones de 868,34 Bs. Posteriormente se realizó los nuevos procedimientos estándares y se planificó como se realizarán las capacitaciones entre capacitaciones en taller o en el puesto de trabajo además de a que operadores se las darán. Con la implementación de las propuestas de mejoras realizadas por la externalización y el análisis ECRS, se obtuvo un excedente de tiempo el cual será un tiempo extra de produccion de 93,43 minutos por cambio de calibre y se realizó una comparación de indicadores financieros y de eficiencia con y sin la implementación del proyecto dado un incremento del indicador de eficiencia GLY de 1,81%, un aumento de la relación beneficio/costo de 0,011 y un incremento de la TIR de 13% con la implementación del proyecto.
Palabras clave
PLANTA SACABA SD, PRODUCTIVIDAD, SMED, EXTERNALIZACION, ANALISIS ECRS, INDICADOR GLY, RELACION BENEFICIO-COSTO.
Metricas del proyecto de grado
Visualizaciones: 1
Agregados a favoritos: 0
Proyectos de grado similares